Why Shouldn’t I Clean Off My Windshield With Hot Water?
With most of our offices being buried under another layer of snow this week, a lot of the employees here at CADimensions are dreading having to shovel out their cars again. Okay, maybe it’s just me, but still! The worst part to me isn’t the shoveling, but having to scrape the ice off both my mirrors and the windshield and rear window of my car. As I sat and watched the snow pile up this morning, I had an idea.
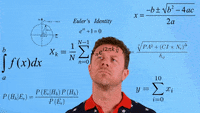
What if I used hot water to melt the ice off of my car in an instant? I wouldn’t have to scrape it off by hand and I’d save myself some time. Now, like any engineer with access to SOLIDWORKS would, I did all my testing virtually first. If you’re not already doing your prototyping virtually, check out my last blog on 5 reasons why you need to run finite element analysis in SOLIDWORKS and why it’s an excellent idea!
Now, the first thing I needed to do was create a model of a windshield, so I modeled something representative of my car’s geometry and assigned a glass material to it:
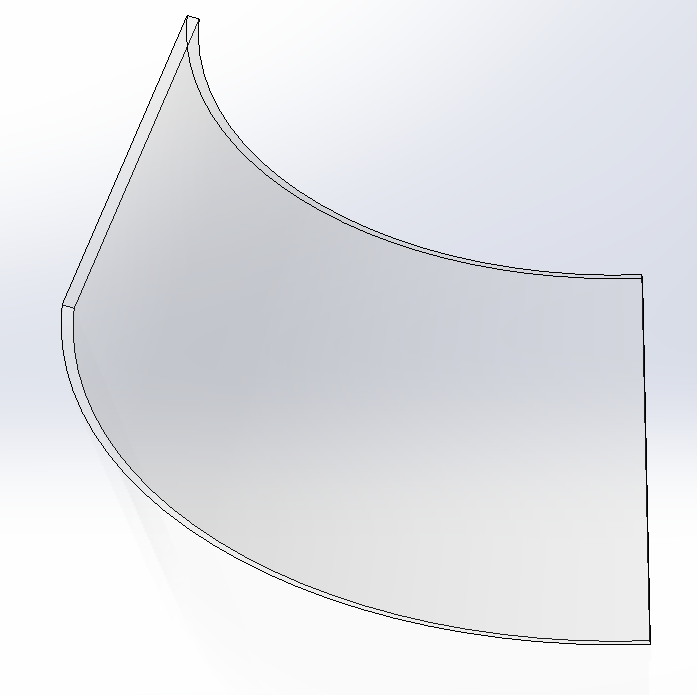
Once I had my CAD model, I created a quick transient thermal simulation to get the temperature distribution in my windshield if I splashed hot water on it. The reason I went with a transient simulation is because I needed to simulate the temperature “shock” as the hot water met the cold glass. I chose a total analysis time of 2 seconds just to see the temperature field develop. I held the glass body at an initial temperature of 20 degrees Fahrenheit, which was the temperature outside my apartment as I was thinking about this problem and my car had been sitting outside all night. At the beginning of the simulation (t=0) I applied a temperature load of 100 degrees Celsius (boiling water) to the front face of my windshield:
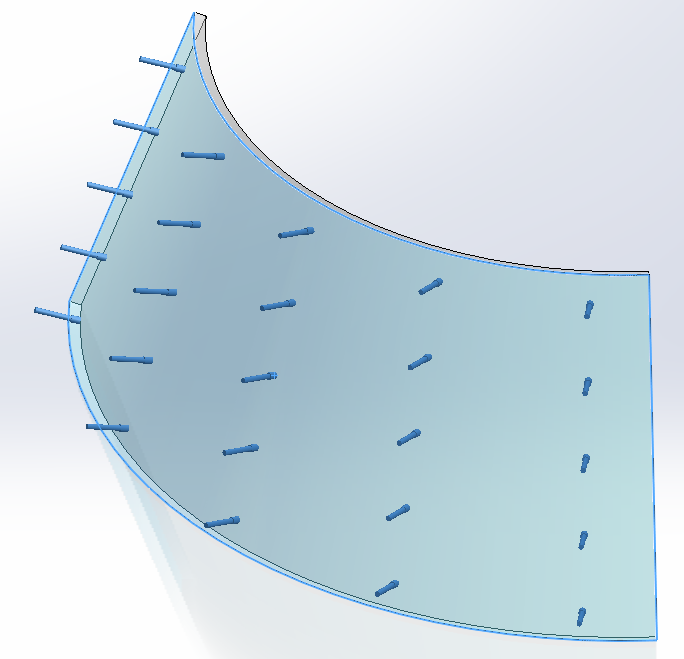
As I expected, I got a great looking temperature distribution through the windshield and things were looking promising!
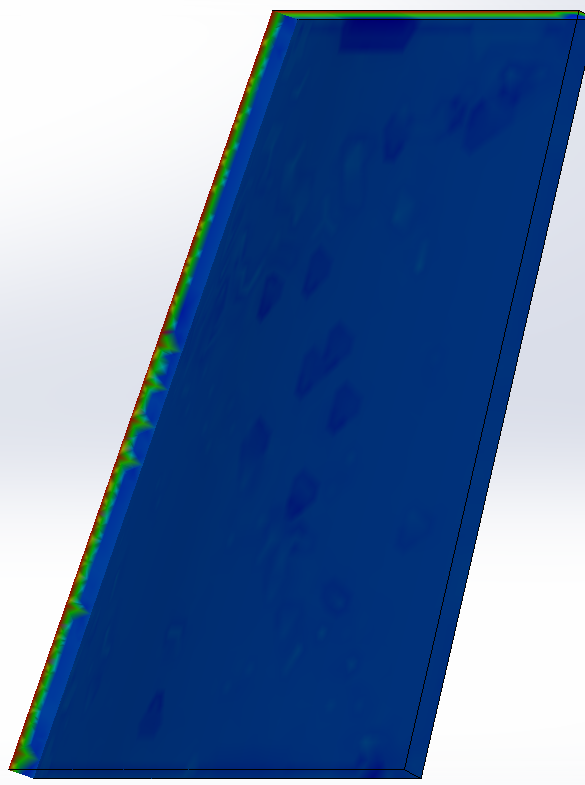
But, that was only step one. The temperature distribution looked good but I still needed to confirm that the residual stress in the glass was below the yield strength so I didn’t do any permanent damage to the part. So I created a non-linear study and used the results of the thermal study as my input. This is the power of SOLIDWORKS Simulation! You can run multiple different types of studies and use them as inputs into other studies to paint the whole picture. The only thing left to do was fix the outside of my windshield where it mounted into the frame:
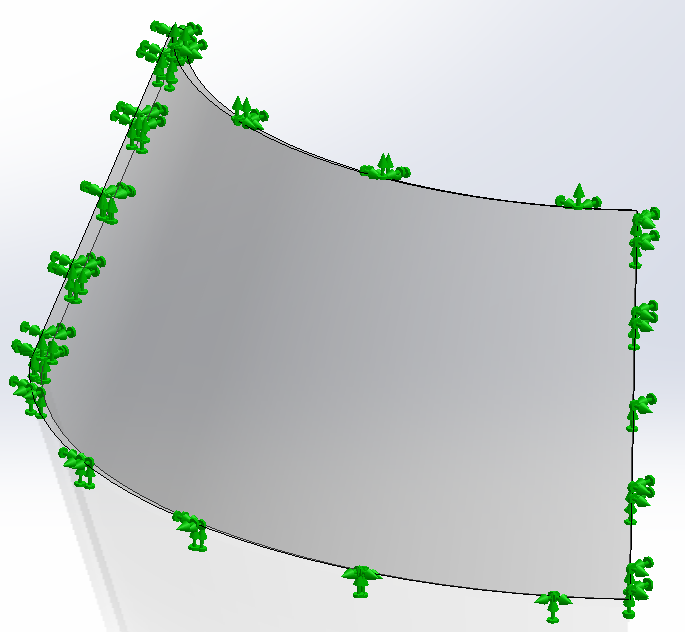
And I was off and running. The tensile yield strength of glass ranges from about 40-70 MPa depending on surface finish and how it’s produced, so to be on the safe side I’ll call my yield strength somewhere in the middle, like 55 MPa. If I take a look at my stress plot from my non-linear study, I can see I might have some issues in my windshield:
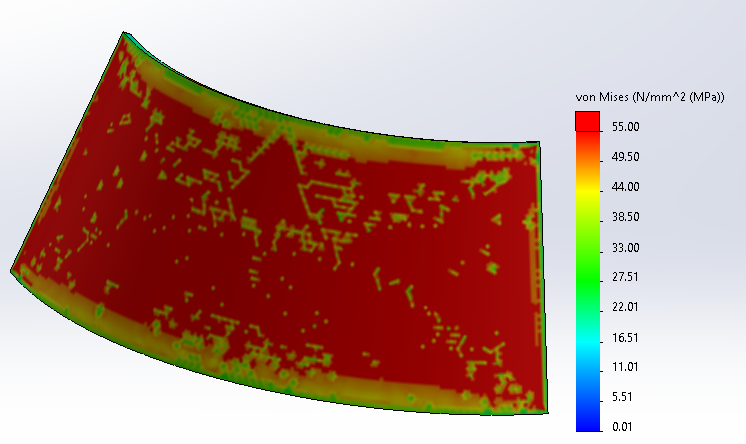
I set the upper limit of my plot to my maximum design stress of 55 MPa, and we can see almost the whole windshield is red, meaning I would have done some serious damage. Good thing I did my testing virtually first!