Sand Casting with FDM Technology
Sand Casting is a metal casting process, using a mold created by depressing a pattern into sand. The pattern imprints a cavity, which is used to cast an array of metal alloys. Sand casting is widely used across many industries to create everything from small items, such as door handles, as well as large components, like engine blocks. Additive manufacturing (AM) has reinvented the traditional practices used in sand casting to reduce cost and increase throughput.
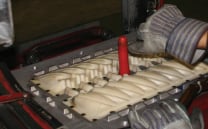
Stratasys FDM technology can be used to circumvent the process of traditional pattern making, which is typically found to be time consuming, costly, and often the leading cause of bottlenecks in production. Through leveraging AM, companies are able to eliminate the need to traditionally machine patterns to create cavities in the sand. This is a realistic alternative due to the compressive strength of FDM parts.
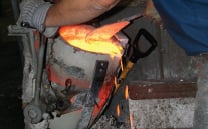
Melron Corporation, a manufacturer of window hardware, utilizes Stratasys FDM technology to achieve high-margin, low-volume production of sand casted parts. Melron has traditionally outsourced the machining of aluminum matchplates for sand casting, a process that was both costly and time-consuming. The adoption of FDM to replace this process leads to a reduction in cost, in addition to decreased lead times for new casting patterns. Dan Schaupp, a manager at Melron, who has embraced the new process, states “FDM is facilitating our transition to new markets by enabling us to produce matchplates at a lower cost and in less time than ever before.”
When asked, Melron Corporation reported the following savings with the switch to FDM sand cast patterns:
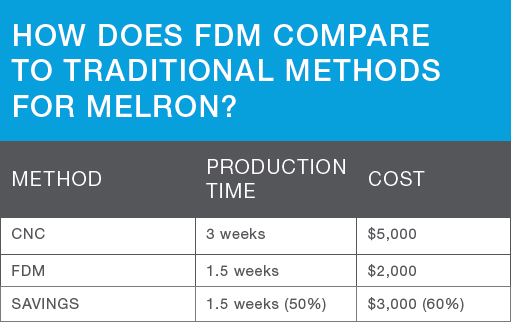
Companies such as Danko Arlington, Rock Island Arsenal and Bradken have also successfully implemented FDM in their sand casting process. As skilled pattern makers become harder to find, companies have found new innovative ways to employ AM to achieve quality sand casted parts. FDM allows manufacturers to deliver precise patterns for the production of sand-casted components.
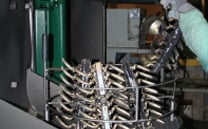