Embracing the Future: On-Demand Production Using Selective Absorption Fusion (SAF) Technology
Selective Absorption Fusion (SAF) technology is reshaping the world of additive manufacturing by pushing the boundaries of on-demand production. While traditional additive manufacturing has already excelled at producing parts quickly and efficiently, SAF elevates this to a whole new level. Let’s dive into what makes SAF unique and explore how it is driving the future of on-demand production.
Understanding the Technology
What is SAF? SAF is an advanced additive manufacturing technology that uses polymer powder as its base material. As a form of powder bed fusion, it involves a unique process in which two print sleds move unidirectionally across the build platform. The first sled deposits layers of powder, each 100 microns thick. The second sled jets a High Absorbing Fluid (HAF) through industrial piezoelectric print heads, allowing the powder to absorb heat via an infrared lamp. This process fuses the powder, layer by layer, creating solid parts. The powder that doesn't absorb HAF acts as support material for intricate geometries and is later removed in post-processing.
SAF Technology Video from Stratasys
Why SAF is Different Unlike other powder bed fusion technologies, SAF’s unidirectional architecture ensures that all parts in the build experience the same thermal conditions. This uniformity leads to more consistent, accurate, and reliable prints, a crucial factor in large-scale manufacturing.
SAF vs. Other 3D Printing Methods SAF sets itself apart from other additive technologies, with its ability to produce parts at high volumes. All 3D printing technologies have their advantages and if you’re looking for high-volume production SAF using the Stratasys H350 3D printer is your best option. SAF can manufacture over 50,000 parts in a short time frame—something other 3D printing methods struggle to match. SAF parts also exhibit near-isotropic mechanical properties, offering superior strength and durability compared to other additive techniques.
Rugby ball printed with SAF technology
The Story Behind On-Demand Production
SAF and High Throughput SAF technology is highly efficient for on-demand production, with a full build taking around 12 hours and a subsequent cooling period, allowing hundreds of parts to be produced in about 36 hours. This speed and flexibility let companies produce exactly what they need, when they need it, minimizing waste.
How It Works Companies using SAF simply import their 3D CAD model into the GrabCAD Print software, nest multiple parts into the build area, and send the job to the printer. The powder acts as support for complex geometries, making the process ideal for producing intricate or customized components. After printing, post-processing via media blaster removes any excess powder, making the parts ready to use or ship within hours.
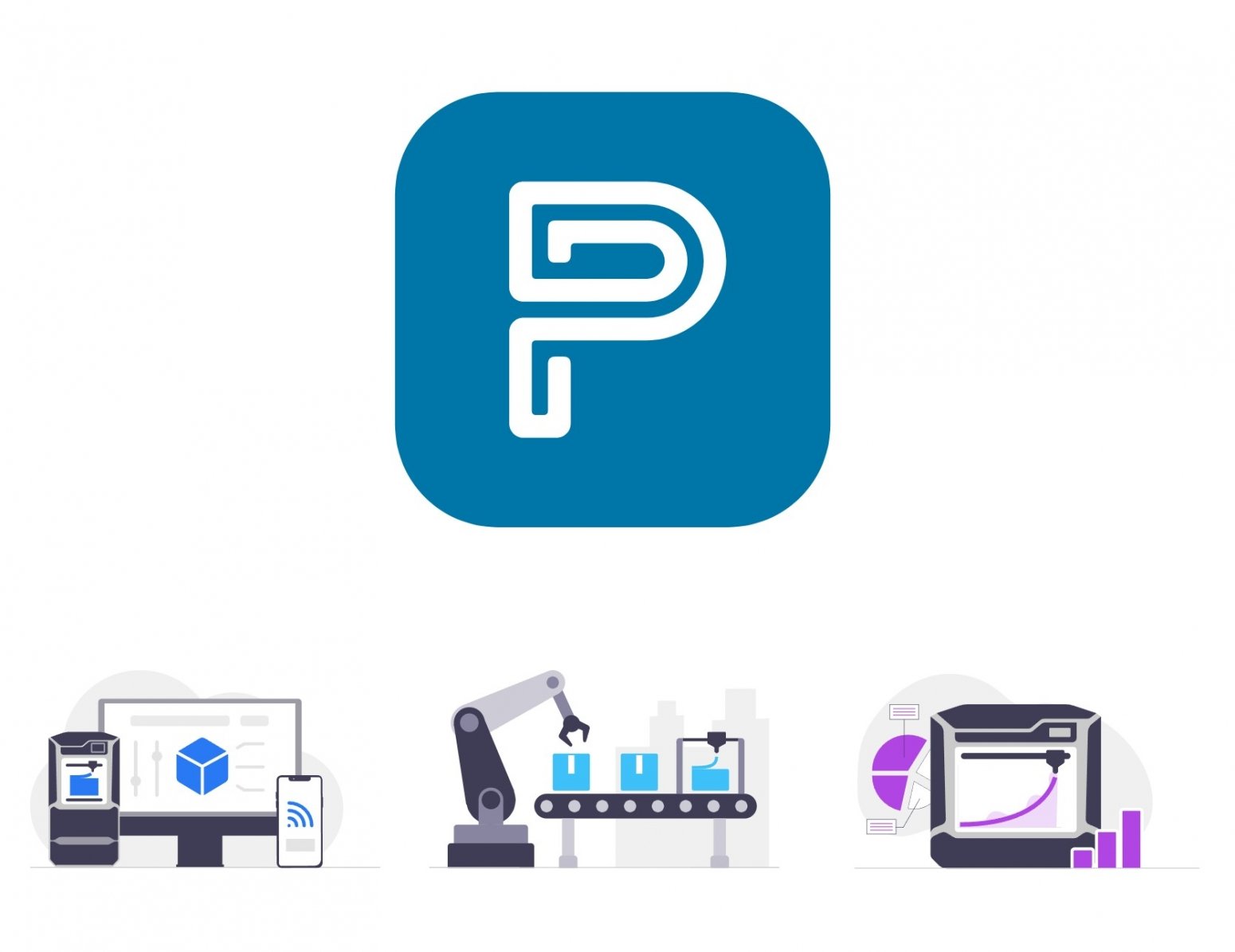
Top 6 Productivity Features Of Grabcad Print Pro
Key Advantages of On-Demand SAF Production
Customized Parts One of the most compelling aspects of SAF technology is its ability to print custom parts with ease. Whether you need one part or 5,000, each part can be unique. This eliminates the need for retooling production lines—a costly and time-consuming process in traditional manufacturing. With SAF, manufacturers can respond to the growing demand for personalized products without compromising efficiency.
Energy Efficiency and Reduced Waste SAF’s on-demand nature ensures that manufacturers only produce what they need. Unused powder can be reclaimed for future builds, reducing material waste and minimizing energy costs. SAF’s energy efficiency is also notable—its energy costs per part are lower than traditional methods like injection molding.
In comparison to traditional injection molding, lead times can be reduced from 12–20 weeks down to just a few days before beginning production. Additionally, in a day or two, a build of spare automotive parts can be ready for distribution. The parking sensor housing below only takes 8.5 hours to produce 270 pieces.” Statasys “How additive manufacturing may just save automotive aftermarket spare parts” blog.
Automotive speaker cover
On-Site Production SAF technology is building momentum in the U.S., particularly for companies looking to reduce their reliance on overseas suppliers and strengthen supply chain stability. On-site production with SAF enables manufacturers to meet deadlines, protect intellectual property, and increase overall operational efficiency.
Preparing for What’s Next
Sustainability Goals SAF technology aligns with broader environmental and sustainability initiatives. Using PA11, a bio-renewable material derived from castor beans, SAF minimizes the carbon footprint of manufacturing. By focusing on producing only what is needed and reclaiming unused materials, SAF helps companies reduce waste and energy consumption.
Upcoming Innovations SAF technology is constantly evolving. For example, Stratasys recently introduced polypropylene, a highly requested material, into the market. Next in line are materials like glass-filled nylon, which will enable even more advanced applications. Additionally, automated post-processing and software advancements like Stratasys’ Streamline Pro are on the horizon, making SAF even more integrated into production workflows.
In Conclusion
As industries push toward more efficient and customizable production, SAF technology is leading the charge in on-demand manufacturing. With its ability to produce high-quality parts quickly and efficiently, SAF represents the future of manufacturing—offering flexibility, sustainability, and reliability that few technologies can match.
Water pump filter printed with polypropylene