3 Ways Smart Work Instructions Build Better Operators
The main reason work instructions go unused is because they don’t add enough value to operators. Instead, they slow them down, having to sift through piles of pages for specific information. This is true for both paper and digital work instructions alike. The answer is an emerging concept called Smart Work Instructions (SWI).
Not all digital work instructions are created equal. Smart Work Instructions can connect with IoT devices, host process logic, and collect valuable data from people and machines. So how does this new form of directions improve life for operators and engineers?
Improve Operator Productivity With Smart Work Instructions
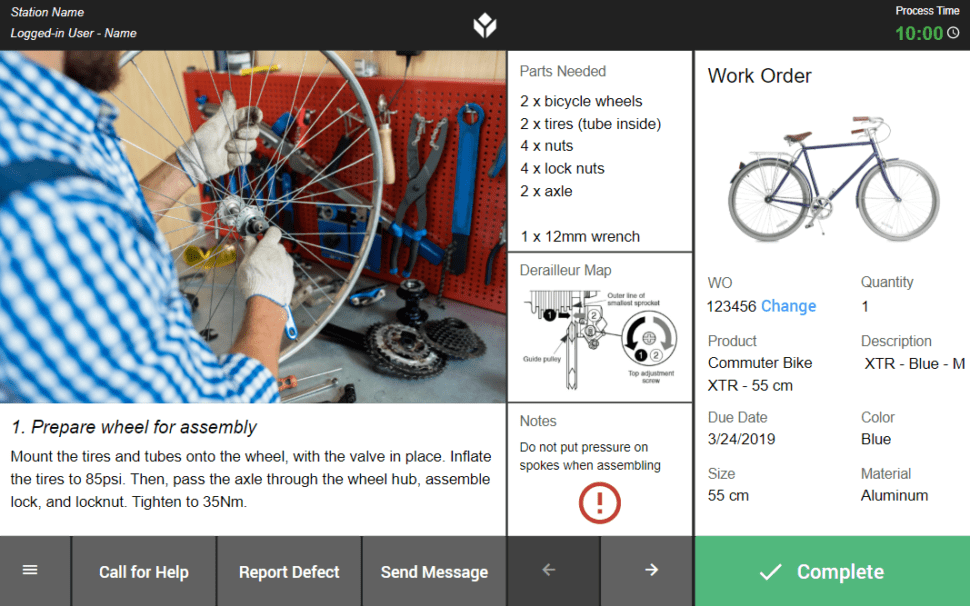
Smart Work Instructions help operators increase their throughput by guiding them through processes to complete them faster. Unlike regular paper directions, SWI flow with operators isn’t slowed down going between directions and assembly.
Additionally, Smart Work Instructions allow managers to identify out-performers and propagate their tribal knowledge to the rest of the team, turning every operator into the best operator.
Smart Work Instructions use logic to prevent mistakes from occurring. For example, maybe an operator is entering a quality control measurement. If an entered value is outside of the tolerance range, the instructions can notify the operator immediately.
Traditional quality control is prone to error. By entering QC data directly into a digital platform, mistakes are prevented. The process will stop the operator and give guidance to fix the issue.
IoT integration with devices like torque drivers and pick-to-light systems can ensure that simple mistakes no longer happen. More advanced applications can even integrate with vision systems like Cognex.
Enables Data Driven Performance Reviews
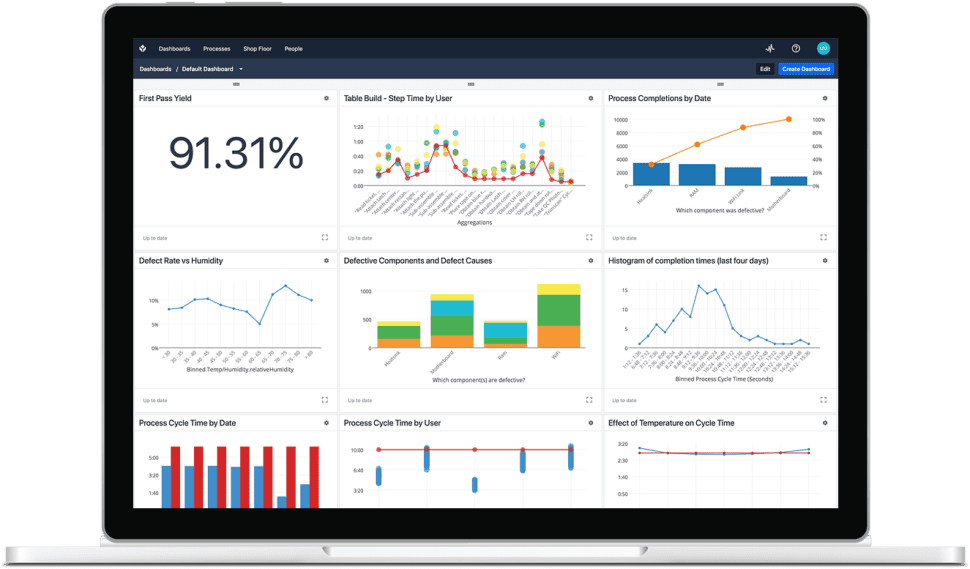
Without smart work instructions, performance reviews are subjective because they lack data. Operator data is sporadically collected by a supervisor. This can vary widely between companies, but can be as rare as once per month. This method does not give managers a full picture of the operator’s performance.
Since smart work instructions collect performance data on a continuous basis, they enable managers to provide real-time targeted feedback to operators and immediately see the impact. It also lets managers and operators have data-driven conversations about performance, which increases the operator’s willingness to improve.
Involve Operators in Continuous Improvement
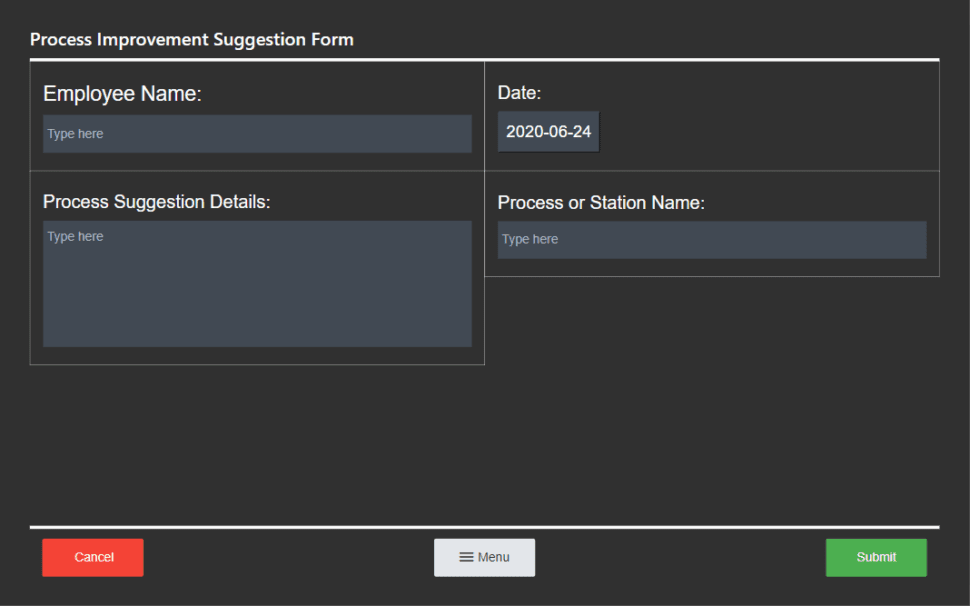
The idea behind Kaizen (continuous improvement) is that all employees are engaged in the regular, incremental development of the company. This involves every employee, from upper management to operators. The issue is that operators often lack the channels to voice their feedback.
SWI addresses this situation by providing a direct channel where operators can give suggestions on a process, empowering them to improve processes and have a measurable impact on the entire operation.
In Summary
The operators and assembly technicians are the heart of any operation. Like any person, they can make mistakes. However, Smart Work Instructions can build operators that are productive, understand their performance, and offer feedback to optimize the process.