How Additive Manufacturing Speeds Up Time from Prototyping to Mass Production
3D printing (additive manufacturing) is becoming a go-to solution for mass production. World manufacturing had already slowed down in 2019 then, in early 2020, it hit a sharp decline when global production dipped due to COVID and supply chain issues.
The scramble began a search for cost-effective and immediate solutions that could circumvent those issues within manufacturing. Thus, conventional factory manufacturing soon turned an eye toward something new, flexible, fast, and affordable: 3D printing.
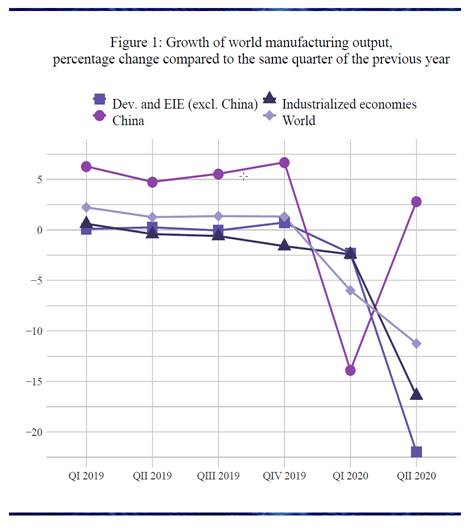
More Results, Less Investments
Rapid prototyping is an integral part of the manufacturing process. Today, 3D printing supplements product development because of its capacity to create strong, highly customized parts on demand and in large amounts.
Companies can now utilize mass production without having to invest hundreds of thousands of dollars in industrial equipment and assembly line employees to put the parts together.
Additionally, by using additive manufacturing, companies can save money by investing less in raw materials. 3D printing reduces the number of raw materials needed to produce a prototype or finished product without losing its structural integrity.
When you remove unnecessary costs and potential prototyping design delays from the equation, the time from prototype to production decreases.
3D Printing, Mass Production, and Customization
For some, the appeal of 3D printing technology outweighs the benefits of using traditional factory manufacturing. Additive manufacturing brings with it a sense of quality in design and conformity, which is essential to creating a solid prototype before it moves into mass production.
Customization is another huge consideration. Typically, customized products are offered in small batches on demand. However, once they have peaked demand by a large enough customer base, additive manufacturing makes it easy to replicate that customization to mass produce it, too.
The customizations that would have taken weeks to produce in a factory are now integrated with a few clicks on a computer— ready to print.
Produce More, Go to Market Faster
From concept to prototype to launch, additive manufacturing helps companies of all sizes produce more and get to market faster. CADimensions 3D printing solutions give companies access to produce goods in high-volume when they need it. That means no more long lead times, producing products with fewer constraints, and cheaper production costs.
We’ve recently acquired the Stratasys H350 SAF Printer, which is one of the newest models on the market. It uses SAF technology to produce engineering-grade parts with precise geometric accuracy. From bulky, complex or simple parts, this Stratasys H350 maintains consistency and power.
Real World Example: How does additive manufacturing compare to traditional methods?
A great example of how one company reduced production time and cost is Robert Seuffer GmbH & Co., based in Germany, manufactures sensors, electronics, and controls for use on finished products in numerous industries. During its quality control process, Seuffer conducts testing to validate the fit and functionality of any potential new part by creating prototypes with metal molds. However, the company’s management was interested in exploring alternatives that would allow them to accelerate the process, and reduce the number of design iterations, before allocating valued resources.
METHOD | COST | PRODUCTION TIME |
Metal Mold* | $52,725 | 56 days |
3D Printed Mold | $1,318 | 2 days |
Savings | $51,407 (98%) | 54 days (96%) |
By using 3D printing, a prototype mold was built in one day and required only three hours of component fitting and assembly. What’s more, the 3d printed mold cost less than $1,400 to produce.